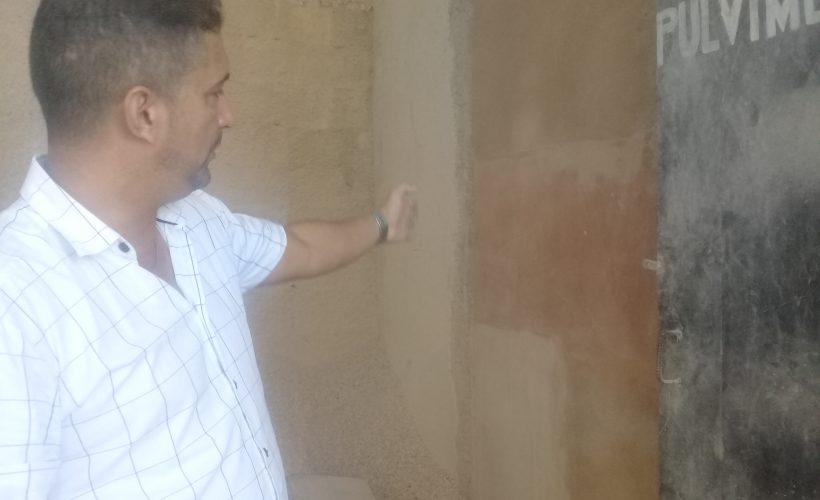
Cuando me hablan de pensar como país, imagino a personas como Rojitas, al que no le alcanza el tiempo para replantearse proyectos, gestionar saberes, insertarse en líneas de investigación que le permitan reciclar y al mismo tiempo ahorrar recursos de gran costo para la Isla.
Con una pasión que contagia, habla sobre las nuevas máquinas que con poco recursos hará o sobre los ensayos que tiene en mente para estudiar los hidrofugantes, algunos aditivos básicos como los aceleradores de fraguado, elementos que de hacerse con la combinación de recursos nacionales y extranjeros pudieran minimizar su precio.
Si lo dejas hablar conocerás sobre otros planes que también ha visualizado como las soluciones para la humedad o los ensayos en materiales que aíslen el ruido y controlen la temperatura.
De todo ello hay rastro al recorrer la pequeña fábrica de materiales de la construcción, nacida en el perímetro de la Universidad de Matanzas. Allí, además de las habituales máquinas y equipos, hay espacio para probetas, tubos de ensayo y pequeños cubos de concreto que ya han servido de estudio.
Por cómo habla, pareciera que Arnaldo Rojas Vergara no entiende de imposibles. Ingeniero civil de profesión, luego de trabajar 15 años en la tercera constructora más grande del mundo, que junto con Arcos asume la explotación hotelera, decidió apostar por el cuentapropismo y se unió a la Constructora Atlántico, una de las 12 primeras cooperativas creadas en Cuba.
“Durante esos años trabajando en la construcción, me di cuenta de que importábamos muchas cosas existentes aquí y empleábamos dinero en transportación y gestión empresarial. Sabía que en todo el mundo las universidades se rodeaban de un polo de desarrollo y en Cuba se habían dado algunos pasos, pero aún no era fuerte”, comenta Rojas Vergara.
Así, cuando en 2020 se empieza a hablar de los proyectos de desarrollo local, se enroló en la nueva iniciativa y creó AR Construcciones y talleres, dedicado a la fabricación de materiales de la construcción y maquinarias.
GÉNESIS DE UN PROYECTO
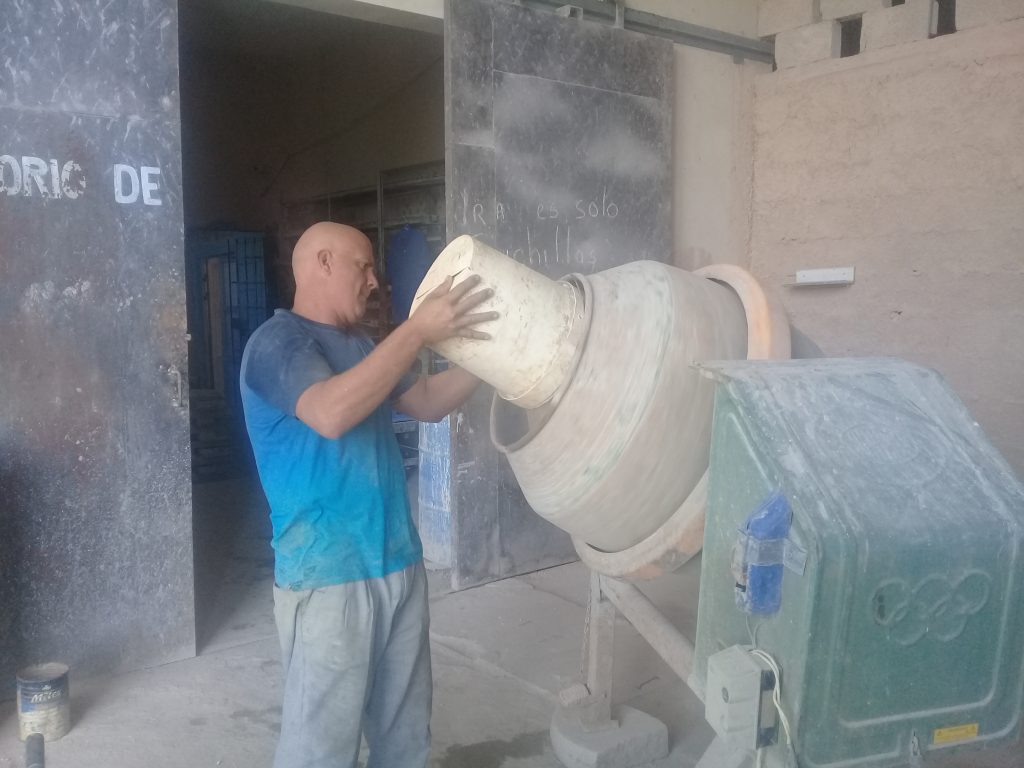
“Supimos de todos los trámites a efectuar a través del delegado de la circunscripción, que ya tenía la experiencia de Alelí. Tras un previo intento para llevar a cabo el proyecto, en el 2021 buscamos otras alternativas y trabajamos a partir de nuestro producto estrella, que son los predosificados.
“Ello consiste en poner dentro de un saco todas las dosificaciones de los materiales que componen el repello fino, el grueso, morteros de colocación de pisos… Así es más fácil venderle a un sector y además se evita el reguero, los malos consumos del cemento en obras y contribuye a la optimización del transporte.
“Con el apoyo de la decana de la Facultad de Ingeniería, empezamos a pasear la Universidad y encontramos este espacio, siempre teniendo claro lo que la ley permite hacer en materia de innovación.
“No fue tan sencillo, porque para crear una pequeña fábrica de materiales debíamos tener cemento. Finalmente se aprueba el 8 de septiembre de 2021, sin la seguridad de contar con este elemento.
“El 6 de abril de 2022, después de tocar varias puertas, llegó la primera tolva, de 200 toneladas asignadas, de la Empresa Comercializadora de Cemento. Con las primeras 20 t pudimos hacer un estudio de cuánto se perdía al enviar el cemento sin dosificar hacia las obras.
“Los resultados arrojaron que a veces se pierden hasta 6 t en obras abiertas de cada 20 y solo se aprovechan correctamente 14, porque se calcula o manipula mal. Aquí todo se calcula, se dosifica y se pone dentro de los sacos por cantidad”, explica Rojas Vergara.
RECICLAR Y AHORRAR, LA CLAVE DEL ÉXITO

En la fábrica donde se elaboran 44 productos y especializada en la confección de morteros de albañilería y reparación, tienen una máxima que consiste en promover la cultura del reciclaje.
No en balde desarrollan, de conjunto con el Centro de Estudio de Fabricación Avanzada y Sostenible de la Universidad de Matanzas, la investigación Reciclaje de la escoria de la soldadura y fundentes a presión, que estudia los posibles usos para la reutilización del residual altamente contaminante y difícil de desintegrar.
Este proyecto, que consiste en reciclar la escoria y emplearla en la fabricación de materiales de la construcción, forma parte del programa territorial Encadenamientos productivos y circuitos cortos de producción-comercialización de bienes y servicios de la provincia de Matanzas, cuyos resultados e impacto tributan al progreso del territorio.
“El profesor Marcelino Rivas realizaba una investigación, a partir de la imposibilidad de la Empresa Conformat de deshacerse de la escoria que generaban, y me pidió ver si en el molino podíamos triturar algunas pruebas.
“Cuando lo hago veo la granulometría y le propongo hacer otros ensayos para utilizarla en nuestros áridos. Él me comenta que existían estudios sobre su empleo en este sector y encuentro que se habían hecho investigaciones con resultados, pero sin continuidad.
“Hicimos varios ensayos, la pusimos dentro del mortero de terminación texturizado y funcionó. A un diseño de mezcla le quitamos un porciento de cemento y lo sustituimos por la escoria. Entonces, nos dimos cuenta de que, al mantener el 80 % de cemento y el 20 de escoria, los índices de resistencia no se movían mucho.
“Obtuvimos resultados que se encuentran entre los parámetros normados en Cuba para los morteros de albañilería. La escoria está compuesta por cinco minerales de los que se oxidan en muy baja proporción; el resto reacciona muy bien con el cemento y genera buena adherencia, alta resistencia y durabilidad.
“Tenemos varias líneas de investigación e innovación abiertas para introducir otros compuestos en nuestras producciones, que nos faciliten el ahorro de productos encarecidos y en falta, como el cemento”, argumenta entusiasmado Rojas Vergara.
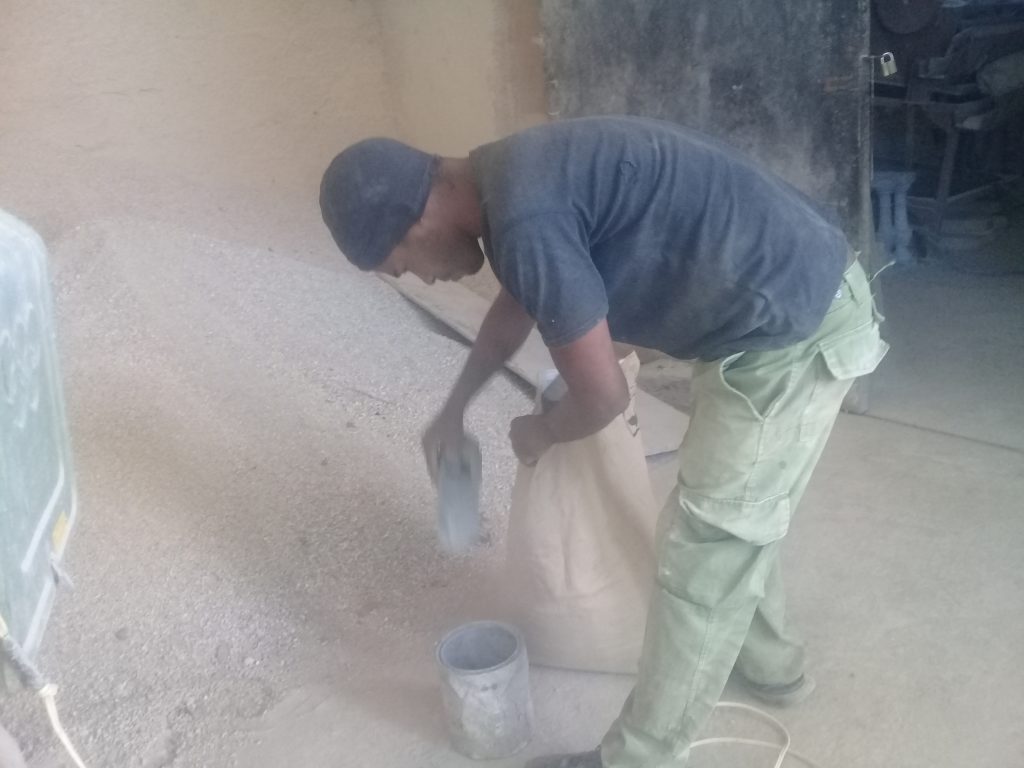
Los materiales producidos a base de escoria en la fábrica enclavada en la Universidad de Matanzas ya han encontrado sus primeros clientes, entre ellos el Estadio Victoria de Girón. Asimismo; producen otros materiales que son adquiridos por el sector residencial y mipymes, a precios más rentables.
Mientras caminamos por la pequeña fábrica, Rojitas comenta que aquí todo se reutiliza, incluso la barredura. “Si pudiéramos evaluar la cantidad de desechos que se generan en el país y se pueden aprovechar en la construcción… Imagínese que hemos solicitado que nos envíen el residuo de la reparación de la Universidad. Lo clasificamos y una parte de nuestros materiales se hacen con eso: los áridos, los bloques; y ello ahorra salario y combustible”.
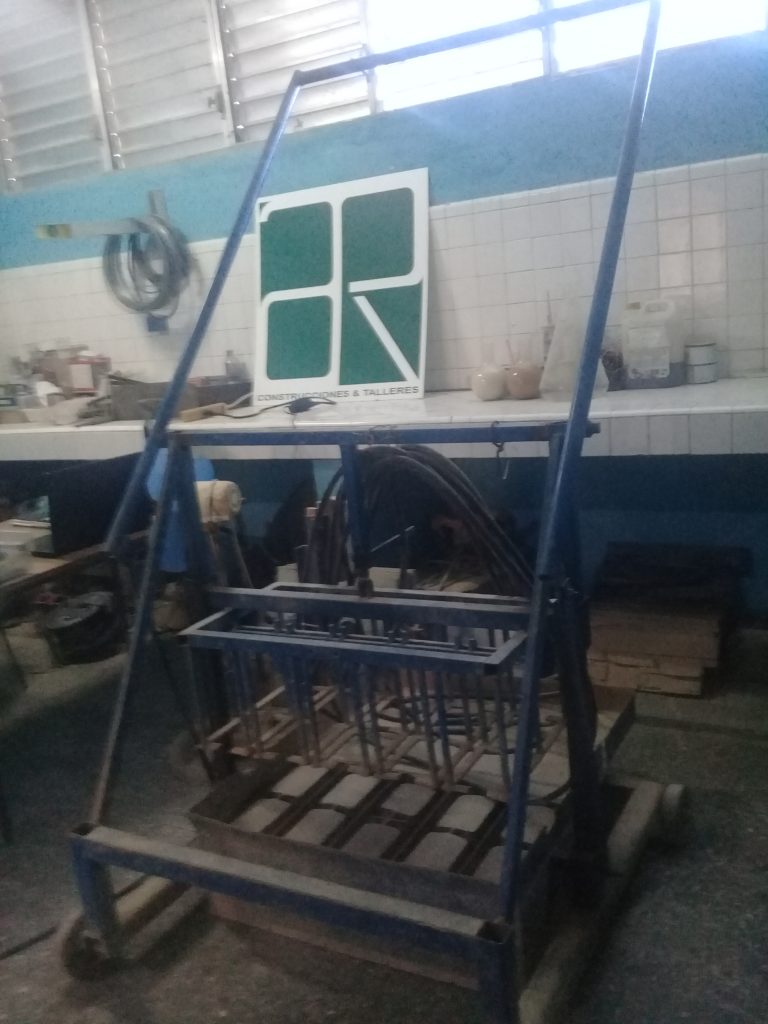
Rojitas es un soñador, de eso no hay duda, pero con los pies bien puestos en la tierra. Lo escucho hablar y pienso en cómo hará para expandirse y combinar la economía del proyecto con la investigación, o para colaborar con los estudiantes de la carrera de Ingeniería Civil o para continuar experimentando con el PVC que genera la fábrica al lado de la suya.
La verdad no sé cómo se las arregla para hacer tantas cosas a la vez. Lo que sí sé es que se necesitan más hombres como él que piensen y sueñen a su país.
Muyyyyyy bien Rojitas, necesitamos a muchos cómo tú en este país!!!!!!